Digital transformation is no longer a buzzword for manufacturers—it’s a business necessity. The shift towards smarter factories, intelligent systems, and data-driven operations is happening fast. For those in the industry, adapting to these changes isn’t just about staying ahead—it’s about staying in business. In this article, we’ll break down 30 key statistics that show just how much digital transformation is changing manufacturing. Each stat is expanded with practical insight and hands-on advice to help you take action today.
1. 91% of manufacturers are investing in digital transformation initiatives
Why it’s happening
The vast majority of manufacturers are putting money into digital initiatives. Why? Because the benefits are obvious—better efficiency, lower costs, faster turnaround, and more agility. In the past, investing in technology was seen as a risk. Today, not investing is a bigger risk.
What this means for your business
If you’re not already investing in digital tools or systems, you’re likely falling behind. This doesn’t mean you need to throw out all your existing systems overnight. Start by identifying your biggest operational pain points. Is it production speed? Inventory management? Workforce training? Match your tech investments to these problem areas first.
Tactical steps to take
- Conduct a digital maturity assessment. Identify where you are today and where the gaps are.
- Create a phased roadmap for investment. Start with tools that offer fast ROI like ERP or MES (Manufacturing Execution Systems).
- Allocate a realistic budget for tech, training, and maintenance.
- Involve your frontline workers early. Their feedback can shape which tools get adopted successfully.
The key takeaway here is that digital transformation is a journey, not a sprint. But you have to be on the path to begin with.
2. 67% of manufacturers have accelerated digital projects due to global disruptions
The pandemic’s impact
COVID-19, supply chain breakdowns, and shifting global politics made it clear—manual processes can’t handle today’s manufacturing complexity. Two-thirds of manufacturers pushed their digital timelines forward as a direct response to these challenges.
The new speed of innovation
Acceleration doesn’t just mean faster project delivery. It also means a shift in priorities. Manufacturers now care more about agility, data access, and automation than ever before. These become the new pillars of a responsive, modern operation.
How to catch up or keep pace
- Prioritize flexibility in your digital systems. Avoid tools that lock you into rigid workflows.
- Choose vendors that can deliver quickly and support integrations with existing tools.
- Build a digital “rapid response” team that can deploy or tweak solutions as needed.
You don’t need to overhaul everything overnight, but you do need to be ready to pivot fast. Agile manufacturing isn’t just a concept anymore—it’s survival.
3. Smart manufacturing technologies can boost productivity by up to 20%
What smart manufacturing actually means
Smart manufacturing combines automation, real-time data, and AI to optimize operations. This isn’t just theory—it’s proven to drive measurable productivity gains of up to 20%.
Making your factory smarter
Start by automating repeatable tasks. Machine monitoring, maintenance schedules, and inventory tracking are great first candidates. Next, feed data into a centralized system so your teams can make better decisions, faster.
Steps to boost productivity
- Invest in sensors and IoT devices for key machinery.
- Use predictive analytics to identify bottlenecks.
- Train staff to interpret machine data and adjust processes in real-time.
- Schedule regular reviews of data to fine-tune production.
With a 20% lift in productivity on the table, it’s worth evaluating your current setup. Even small changes, when powered by smart tools, can lead to huge gains.
4. 76% of manufacturers report improved operational efficiency after adopting IoT
How IoT is transforming the shop floor
The Internet of Things (IoT) connects machines, people, and systems. For three-quarters of manufacturers, this has directly improved how efficiently their operations run. The real power of IoT is in visibility—you can see what’s happening in real time, and act on it.
Use cases that deliver fast results
IoT helps with machine maintenance, quality control, and environmental monitoring. For example, sensors can alert you before a machine breaks down or when temperatures go out of range—helping avoid downtime or defects.
Getting started with IoT
- Choose one pilot area like a production line or warehouse.
- Install sensors and monitor data for trends.
- Set up alerts for unusual behavior to act before problems grow.
- Scale gradually once you prove ROI in one area.
IoT doesn’t have to be overwhelming. When used smartly, it gives you control over your plant like never before.
5. Predictive maintenance using AI can reduce maintenance costs by 25%
Reactive vs. predictive
Traditional maintenance waits for something to break. Predictive maintenance uses AI to analyze data and tell you when something’s about to break. That shift can save you up to 25% on maintenance costs.
What it looks like in practice
You don’t just replace parts on a schedule anymore. You replace them when data tells you they’re worn or likely to fail. This saves money and avoids unexpected breakdowns.
How to implement predictive maintenance
- Start with high-value equipment prone to failure.
- Collect historical and real-time data (vibration, temperature, pressure).
- Use AI tools to analyze trends and forecast issues.
- Create automatic work orders when a potential issue is flagged.
Predictive maintenance is a low-risk, high-reward entry point for digital transformation. Plus, it delivers fast savings.
6. Digital twins can improve product development time by up to 30%
What is a digital twin?
A digital twin is a real-time digital replica of a physical process, system, or product. It lets you simulate, test, and tweak designs before anything physical is built. The result? Product development becomes much faster and more cost-effective.
How it reduces development time
By modeling your design digitally, you eliminate much of the trial-and-error phase. You can find flaws, run stress tests, and even simulate customer use. With all this happening virtually, iterations are quicker and more informed.
How to apply this in your operations
- Use 3D modeling tools to build digital twins of new products.
- Simulate real-world use and gather data from existing products to improve the twin.
- Involve engineers and production teams early to refine designs before physical production begins.
Think of it like a test drive before manufacturing. With a 30% cut in development time, digital twins can help you get products to market faster and with fewer surprises.
7. 60% of manufacturers are currently using or planning to use AI and machine learning
Why AI is becoming a must-have
AI and machine learning can identify trends, make predictions, and automate decision-making across all areas of manufacturing. This isn’t just about robots—it’s about using data smartly to improve performance.
Practical applications of AI in manufacturing
- Forecasting demand based on market and production data
- Optimizing production schedules
- Detecting anomalies in quality control
- Automating inventory restocking
How to begin integrating AI
- Start with data. Clean, structured data is key to any AI tool.
- Use off-the-shelf AI tools in specific areas like quality control or scheduling.
- Build internal AI literacy through training or partnerships.
AI is not science fiction anymore. If 60% of the industry is on board, the competitive pressure to adopt it is real.
8. 80% of manufacturers using cloud-based platforms report faster decision-making
Cloud isn’t just for storage
Cloud-based platforms give everyone access to the same data, wherever they are. That shared visibility helps teams collaborate faster and make decisions with more confidence.
What faster decision-making looks like
Instead of waiting hours (or days) for reports, teams can access dashboards in real time. Operations managers know what’s happening on the floor. Executives see financials. Sales knows what’s in stock.
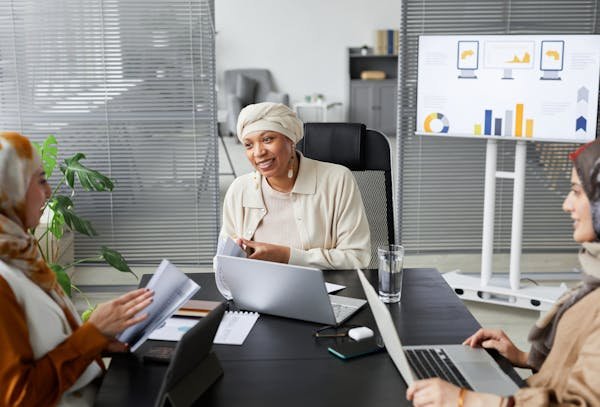
Steps to move operations to the cloud
- Choose a reliable cloud partner that understands manufacturing.
- Migrate non-sensitive data first to get comfortable.
- Implement access controls and staff training.
- Focus on collaboration tools, analytics, and process automation.
Speed is power in business. Cloud gives you that speed without the need for massive infrastructure investments.
9. 85% of top-performing manufacturers use real-time monitoring solutions
Real-time data = real-time control
Top manufacturers don’t wait until the end of the day—or the week—to see how things are going. They use real-time monitoring to get a live feed of performance metrics.
The benefits of real-time visibility
- Spot problems early (before they snowball)
- Optimize line efficiency
- Improve machine uptime
- Monitor energy usage
How to set up real-time monitoring
- Install sensors and connect them to a central dashboard
- Focus first on your most critical KPIs (e.g., output, downtime, waste)
- Set alerts so managers can take immediate action
You can’t improve what you don’t measure—and you can’t fix what you don’t see. Real-time monitoring gives you that visibility.
10. Robotics adoption in manufacturing has increased by 12% annually since 2016
Why robots are taking off
Robots are getting smarter, safer, and cheaper. From welding to assembly to packaging, automation is no longer just for the big players.
What kind of robots are being used
- Industrial arms for repetitive tasks
- Automated guided vehicles (AGVs) for material handling
- Collaborative robots (cobots) that work alongside humans
How to adopt robotics in your plant
- Identify labor-intensive or repetitive tasks first
- Choose a robotics vendor that offers support and training
- Start small with one line or process
- Evaluate ROI continuously
A 12% growth rate is no joke. If you haven’t explored robotics yet, now’s the time to consider where it fits in your operation.
11. 70% of companies that adopted Industry 4.0 tools report improved quality control
What are Industry 4.0 tools?
These include sensors, cloud computing, AI, machine learning, and smart devices. Together, they create a connected, intelligent production environment.
How they improve quality
With real-time data and AI, you can spot defects faster, isolate root causes, and continuously improve quality without manual inspections.
Putting Industry 4.0 into action
- Use vision systems for visual inspections
- Analyze quality data trends to make process changes
- Automate data collection for compliance and reporting
Quality issues can kill customer trust. Industry 4.0 tools make sure your products are right the first time, every time.
12. 58% of manufacturers cite cybersecurity as a top concern in digital transformation
Why security is a growing issue
As you digitize operations, your exposure to cyber threats increases. Systems are more connected, and attackers know manufacturers often lag in IT security.
Common vulnerabilities
- Outdated software on machines
- Unsecured IoT devices
- Weak passwords or user controls
- Lack of employee training
How to protect your operations
- Perform regular security audits
- Invest in network segmentation for critical systems
- Educate all employees on cyber hygiene
- Partner with cybersecurity experts for ongoing support
A breach could mean days of downtime or lost IP. If over half the industry is worried, it’s time to get serious about digital protection.
13. Digital supply chain integration improves lead time by an average of 35%
Why speed matters in supply chains
In today’s world, customers want everything faster. Whether it’s raw materials or finished goods, speed is a competitive edge. Digitally integrated supply chains give you real-time visibility, reduce bottlenecks, and allow for quicker decisions.
How it actually works
With integrated systems, your suppliers, logistics providers, and internal teams are all on the same page. Orders, deliveries, and inventory updates happen in real time. There’s less paperwork, fewer delays, and more control.
How to integrate your supply chain
- Start with a cloud-based supply chain management tool
- Encourage key partners to adopt compatible digital systems
- Set up shared dashboards and data feeds
- Use predictive tools to forecast demand and prevent shortages
Cutting lead times by over a third gives you an edge your competitors will struggle to match. It also improves customer satisfaction and reduces working capital needs.
14. 74% of manufacturers use ERP systems for digital transformation
What ERP does for you
Enterprise Resource Planning (ERP) systems centralize your data. They connect sales, finance, production, HR, and supply chain into one cohesive platform. This enables smoother coordination and better planning.
Why so many are adopting ERP
ERP gives manufacturers better control and real-time visibility. It helps with planning production schedules, managing costs, and tracking inventory more accurately. When integrated properly, ERP becomes the digital backbone of your operation.
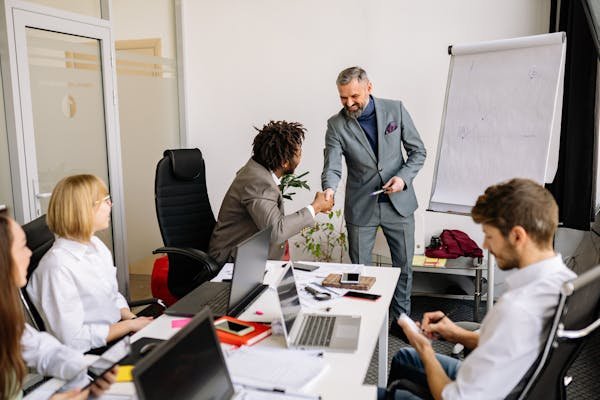
Tips for successful ERP implementation
- Choose an ERP designed specifically for manufacturing
- Focus on the modules that solve your biggest problems first
- Train users thoroughly—poor adoption ruins good software
- Plan for continuous optimization, not just setup
ERP can feel complex, but its payoff is huge. With nearly three-quarters of manufacturers on board, this is a tool that’s proving its worth every day.
15. Paperless operations have increased productivity by 15% across multiple plants
Paper is slowing you down
Manual forms, printouts, and hand-written notes waste time. They’re also error-prone. Going paperless speeds up data entry, reduces duplication, and gives your team more time to focus on value-added work.
What going paperless looks like
- Tablets on the factory floor instead of clipboards
- Digital checklists, reports, and work instructions
- Instant communication via mobile apps
- Automated data logging instead of manual entry
How to go paperless
- Identify high-volume paper processes (e.g., inspections, maintenance logs)
- Use simple mobile forms to replace them
- Integrate digital documents with your ERP or MES
- Provide basic tech training to frontline workers
With a 15% productivity gain up for grabs, going digital with documents is a quick win. It also makes audits, reporting, and compliance easier.
16. 66% of smart factories experience at least 10% increase in throughput
What is throughput?
Throughput is how much product you produce in a given time. Smart factories use automation, data, and integrated systems to remove bottlenecks and boost that number significantly.
How smart factories achieve more
They eliminate delays by making machines talk to each other. They optimize material flow, reduce downtime, and automate decision-making. The result is smoother operations and more output.
Building your own smart factory
- Use sensors and IoT devices to monitor line speed and uptime
- Integrate systems like MES, ERP, and warehouse management
- Analyze performance data to spot slowdowns and fix them quickly
Even a 10% throughput boost can lead to big revenue gains, especially in high-volume environments. Smart factories are designed to make this happen by default.
17. 59% of manufacturers using AR/VR report improved training outcomes
How AR/VR transforms training
Augmented and virtual reality offer immersive, hands-on training without needing to stop actual production. Workers learn faster and retain more because the experience is interactive and realistic.
Where it works best
- Onboarding new employees on complex equipment
- Safety training without real-world risks
- Skill-building for maintenance and repair tasks
Getting started with AR/VR
- Partner with vendors who offer off-the-shelf training modules
- Focus on high-risk or high-complexity processes first
- Equip your training rooms with VR headsets and controllers
Training is often overlooked in transformation. But smarter, more confident workers deliver better results—and AR/VR helps you train at scale with less cost and risk.
18. 80% of industrial IoT (IIoT) users say it gives them a competitive edge
Why IIoT matters
IIoT is all about connected machines, sensors, and systems. It turns your factory into a data-rich environment where you can monitor, predict, and optimize every process.
The competitive benefits
- Real-time decision-making
- Predictive maintenance
- Faster production cycles
- Fewer quality issues
Tapping into IIoT
- Identify processes with lots of manual oversight
- Start by connecting machines that already output data
- Use simple dashboards to visualize insights
The majority of companies using IIoT say it helps them outperform rivals. If you want to lead—not follow—it’s time to plug in.
19. Cloud computing adoption in manufacturing is at 65% and growing
Why manufacturers are moving to the cloud
Cloud platforms offer scalability, flexibility, and cost savings. You don’t need expensive on-premise servers. Plus, you can access data and systems from anywhere—ideal for remote work or multiple facilities.
What to move to the cloud
- ERP systems
- Production scheduling tools
- Quality management systems
- Supply chain management platforms
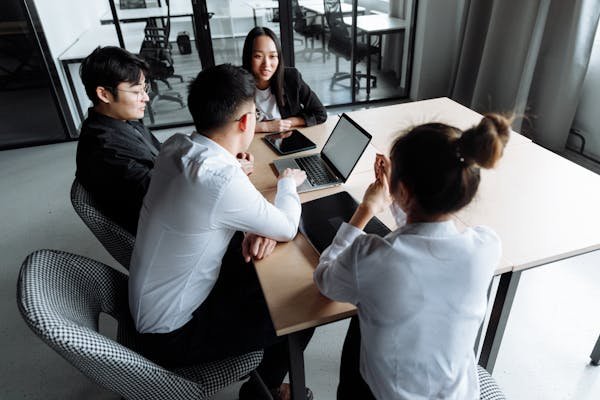
Tips for a smooth cloud migration
- Choose cloud providers that specialize in manufacturing
- Start with non-critical systems
- Plan your migration in phases
- Train your team on new workflows and access methods
Cloud isn’t a trend—it’s the new foundation. With two-thirds already there, the rest will need to move soon or risk falling behind.
20. 69% of manufacturers believe digital transformation is key to future growth
Why growth depends on digital
Growth used to come from adding more machines or people. Now it comes from doing more with what you have. That means better processes, smarter decisions, and faster delivery—all enabled by digital tools.
Digital strategies that support growth
- Data analytics for spotting market trends
- Automation to scale output
- Smart planning to reduce costs and lead times
Laying your digital foundation for growth
- Align your tech roadmap with business goals
- Appoint a digital transformation leader or task force
- Measure progress using real metrics (e.g., OEE, customer lead time)
Almost 70% of manufacturers see digital as essential to growing in the next decade. If growth is your goal, digital is your fuel.
21. 64% of firms use real-time analytics to enhance supply chain resilience
The new reality of supply chains
Disruptions are the new normal. From port delays to raw material shortages, your ability to adapt quickly depends on how well you can see what’s happening. That’s where real-time analytics comes in.
How it makes a difference
Real-time analytics lets you monitor every part of your supply chain. You can spot delays, respond to shifts in demand, and reroute shipments instantly. It’s like having a live dashboard for everything that matters—suppliers, logistics, inventory, and beyond.
How to build supply chain resilience
- Invest in tools that show real-time inventory and shipment data
- Set up alerts for changes in lead times or costs
- Use predictive analytics to prepare for potential disruptions
- Collaborate with suppliers using shared data platforms
When two-thirds of firms are already doing this, you can’t afford to rely on guesswork. Real-time insights are a safety net—and a competitive edge.
22. 45% reduction in energy costs seen with smart energy management systems
Why energy efficiency matters now more than ever
Energy is one of the highest costs in manufacturing. Rising prices and sustainability goals are pushing companies to find smarter ways to manage it—and digital tools are delivering serious results.
How smart systems work
These tools monitor energy use in real-time and adjust systems automatically. For example, they can power down idle equipment or shift energy usage to off-peak hours.
Making your plant energy-smart
- Install energy meters at major equipment points
- Use software to analyze consumption patterns
- Set rules for automated shutdowns and adjustments
- Benchmark against past performance to track savings
Cutting nearly half your energy bill is a game-changer. Smart energy isn’t just for sustainability—it’s for your bottom line too.
23. Digital thread implementation improves traceability by over 40%
What is the digital thread?
It’s the seamless flow of data across the lifecycle of a product—from design and production to delivery and service. It connects everything and keeps a digital record every step of the way.
Why traceability matters
In regulated industries like aerospace, automotive, and pharma, being able to trace every component is essential. But even in general manufacturing, it helps improve quality, compliance, and customer trust.
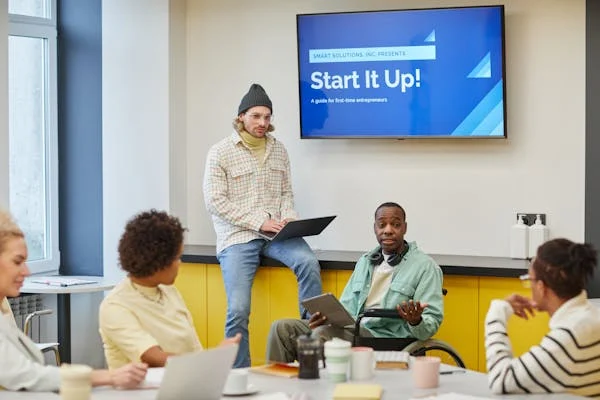
How to implement a digital thread
- Standardize data formats across your systems (PLM, ERP, MES)
- Use barcoding or RFID to track components through each stage
- Make records easily accessible and searchable
- Integrate design and production data so changes are tracked end-to-end
When you know exactly what went into every product—and when and how—it makes audits, recalls, and improvements much easier.
24. 78% of manufacturers report better customer satisfaction through digital initiatives
How digital boosts customer satisfaction
It’s not just about making things faster or cheaper. It’s about delivering exactly what your customers want—on time, every time. Digital tools help you meet deadlines, maintain quality, and offer visibility that builds trust.
What customers care about
- Consistent lead times
- Accurate order tracking
- Rapid response to changes or issues
- Reliable product performance
What to do right now
- Implement order tracking tools your customers can access
- Use CRM software to understand customer needs and history
- Offer faster quoting and delivery options powered by real-time data
Digital transformation isn’t just internal. When it makes life easier for your customers, it builds loyalty that lasts.
25. Adoption of cobots (collaborative robots) has increased by 23% in 3 years
Why cobots are different
Unlike traditional robots, cobots are designed to work safely alongside people. They’re flexible, easy to program, and ideal for small-batch or varied work. Their rise in popularity isn’t surprising.
Where cobots shine
- Assembly tasks with high variability
- Machine tending
- Packaging and palletizing
- Quality inspections
How to start using cobots
- Choose tasks that require precision but not speed
- Work with a vendor that offers training and integration help
- Test on one line before scaling across the factory
With a 23% growth rate, cobots are showing they can increase output while keeping humans in control—literally side-by-side.
26. 82% of manufacturing executives see smart factories as critical to competitiveness
The new standard for manufacturing
Executives aren’t dreaming—they’re planning. The vast majority believe smart factories are not just helpful, but essential to staying competitive.
What defines a smart factory
- Real-time data flowing between systems
- AI-driven decision-making
- Automated processes with minimal manual intervention
- Constant optimization based on analytics
How to build your smart factory vision
- Start with digital basics—connect systems and collect data
- Identify processes ripe for automation or optimization
- Use pilot projects to test smart tools
- Expand and improve continuously
If most leaders see this as the future, then the time to build that future is now. Smart factories are no longer optional—they’re expected.
27. 50%+ of manufacturers use mobile apps to support factory operations
Why mobile matters on the shop floor
Speed matters—and mobile apps provide it. Whether it’s scanning inventory, checking machine status, or reporting an issue, apps bring instant access and action to every corner of your operation.
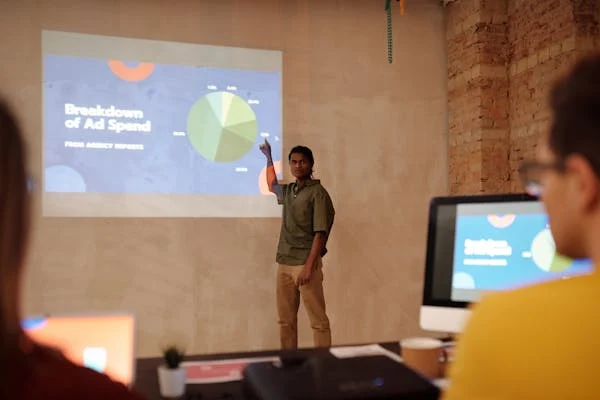
Common mobile use cases
- Maintenance alerts and reporting
- Quality inspections and issue logging
- Time tracking and shift handovers
- Inventory scanning and adjustments
How to introduce mobile tools
- Choose apps that integrate with your existing systems
- Keep the interface simple and intuitive
- Provide training and support devices where needed
- Measure usage and gather feedback regularly
Half the industry already sees the power in their pocket. If you’re not mobile yet, start with one app and scale from there.
28. 33% improvement in product innovation speed due to digital R&D tools
Innovation depends on tools
Developing new products isn’t just about ideas—it’s about execution. Digital R&D tools speed up prototyping, testing, collaboration, and design changes, allowing you to launch faster.
Examples of digital R&D tools
- CAD software integrated with simulation tools
- PLM (Product Lifecycle Management) systems
- Cloud-based collaboration platforms for engineering teams
How to innovate faster
- Use digital simulation to test before prototyping
- Shorten design cycles by enabling parallel collaboration
- Archive and reuse past designs to cut development time
With a third more speed in your innovation cycle, you can win market share before your competitors even launch.
29. 55% of manufacturers use digital dashboards for KPI tracking
Why dashboards matter
When you can see your performance in real-time, you can steer the business better. Digital dashboards help you track KPIs across production, quality, maintenance, and delivery.
What makes a great dashboard
- Real-time data feeds
- Simple, clean layout
- Role-specific views (e.g., operator vs. plant manager)
- Clear targets and alerts
How to implement dashboards
- Identify the most important KPIs for each team
- Use software that integrates with your existing systems
- Set up automated data pulls and update intervals
- Train users to interpret and act on the information
Dashboards take the guesswork out of management. They make performance visible—and improvement achievable.
30. 68% of manufacturers plan to invest in edge computing in the next 2 years
What is edge computing?
It means processing data at the source—right on the machine or device—rather than sending everything to the cloud. It’s faster, more secure, and ideal for real-time decisions.
Why it’s gaining momentum
- Lower latency = faster reaction times
- Less data sent to the cloud = lower costs
- Local control = more reliability during outages
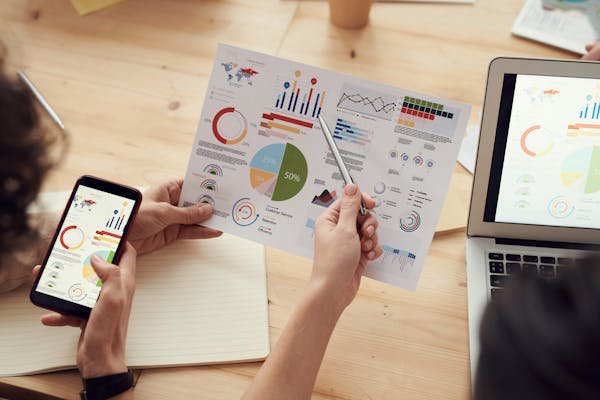
How to prepare for edge computing
- Choose machines and systems that support edge-ready devices
- Start with use cases that need immediate response (e.g., machine control)
- Work with IT and OT teams to ensure secure integration
Edge computing is the next frontier of smart manufacturing. If 68% of your peers are planning for it, it’s time to add it to your roadmap.
Conclusion
Digital transformation in manufacturing isn’t about following trends—it’s about solving real problems and unlocking real opportunities. These 30 stats aren’t just numbers. They’re proof that the industry is changing fast, and the time to act is now.