Cold chain logistics is no longer just about moving perishable goods. It’s about precision, innovation, and reliability. The world is demanding faster deliveries, safer products, and smarter technology—and the cold chain industry is rising to meet that challenge. In this article, we’re diving deep into the top 30 stats that define where the industry is headed. For each stat, we’ll break down what it means, why it matters, and what actions you should be taking. If you’re a logistics business, food company, pharmaceutical brand, or tech investor, this guide is your blueprint for navigating the fast-evolving cold chain world.
1. The global cold chain logistics market was valued at $286 billion in 2022 and is expected to reach $801 billion by 2032
A booming market
Cold chain logistics has become one of the fastest-growing sectors in the global supply chain industry. A jump from $286 billion to $801 billion shows how deeply reliant industries are on refrigerated transport and storage. The surge is driven by increasing global trade, rising demand for perishable goods, and healthcare expansions. It’s not just a trend — it’s the future of shipping and storage.
What’s behind the growth?
There are three key reasons:
- Globalized food trade: More people are eating imported fruits, vegetables, and meat. These need refrigeration across the journey.
- Pharma needs: Vaccines and biological drugs require strict cold storage.
- E-commerce: Customers now expect fresh groceries and medicines delivered quickly and safely.
What should your business do?
If you’re in shipping, manufacturing, or retail, now’s the time to think long-term. You should:
- Invest in cold storage infrastructure — Warehouses and mobile refrigeration units will only become more essential.
- Get certified — International certifications such as GDP (Good Distribution Practices) and HACCP help you stand out in a competitive market.
- Partner smartly — Work with cold chain logistics providers who understand your niche — be it food, pharma, or chemicals.
By 2032, the winners in this space will be the ones who prepared early. Don’t wait to modernize.
2. The market is projected to grow at a CAGR of 10.5% from 2023 to 2032
What does CAGR tell us?
CAGR, or Compound Annual Growth Rate, shows how steadily an industry is expanding. A rate of 10.5% is significant — it means cold chain logistics isn’t growing in fits and starts. It’s gaining ground year after year. And not many logistics sectors can boast such consistency.
What’s fueling this pace?
- Technology: Automation, AI, and IoT are helping companies streamline operations.
- New regulations: Governments are tightening controls on food safety and pharmaceutical transportation.
- Urbanization: Cities need faster, smaller cold deliveries to stores and homes.
How can you ride this wave?
This kind of stable growth presents an excellent opportunity to plan strategically:
- Diversify your cold offerings — Frozen, chilled, and ultra-cold logistics all have different use cases.
- Scale gradually — With predictable growth, you don’t need to over-invest. A step-by-step expansion works.
- Secure financing — Show these numbers to potential investors or banks. They highlight your industry’s stability.
The cold chain isn’t just hot right now. It’s warming up for a long run.
3. Pharmaceuticals account for 30% of global cold chain logistics demand
Pharma and the cold chain
Pharmaceuticals are sensitive. From insulin to vaccines to cell therapies, many life-saving medicines must be kept within strict temperature ranges. No wonder they account for nearly one-third of global cold chain use.
What this means for logistics players
Handling pharma is not like handling frozen meat. It requires:
- Strict temperature control (usually 2–8°C, but sometimes below -70°C)
- Clean, contamination-free environments
- Traceability and audit trails
If you’re a logistics company, pharma logistics is a high-reward, high-responsibility game. But the rewards are immense.
Practical tips for pharma readiness
- Train your staff — Every handler must know temperature sensitivity basics.
- Use validated packaging — Passive and active containers need to be pre-tested and approved for pharma use.
- Adopt digital tracking — A good visibility platform helps catch issues before they become costly.
Don’t treat pharma like any other cargo. Precision is everything.
4. Over 20% of temperature-sensitive products are damaged due to improper cold chain practices
The cost of carelessness
This is a painful stat. Imagine 1 in every 5 sensitive items — be it seafood, cheese, or medicine — arriving spoiled. That’s lost revenue, wasted product, and a damaged reputation.
Common causes of damage
- Temperature fluctuations — Even brief exposure can trigger spoilage.
- Packaging failures — Cheap containers or poor insulation lose their chill fast.
- Delays — A shipment stuck at a border or on the tarmac can quickly warm up.
How to fix the cracks
- Audit your cold chain regularly — Run mock shipments to test your systems.
- Use time-temperature indicators (TTIs) — These small stickers help detect any breach.
- Build in redundancy — A backup power source or alternate truck route can be a lifesaver.
In cold chain logistics, being perfect is not a luxury — it’s a requirement.
5. 60% of vaccine shipments face temperature excursions during transportation
A serious vulnerability
This stat is eye-opening. Vaccines are delicate biological products. A temperature excursion, even if temporary, can destroy their efficacy. And yet, more than half the shipments experience this risk.
Why is this happening?
- Poor handling during loading/unloading
- Uncalibrated refrigeration systems
- Lack of real-time temperature tracking
Most excursions happen in the “last mile” — the final leg from hub to clinic.
What must change?
- More use of GPS-enabled sensors — So you know if a shipment went outside the safe range.
- Better driver training — Human error is still the top cause of vaccine cold chain failures.
- Tighter partnerships — Work closely with vaccine manufacturers to understand product-specific needs.
Trust is the backbone of the healthcare supply chain. And temperature trust must be earned.
6. North America represents around 35% of the global cold chain logistics market
A regional powerhouse
North America, particularly the U.S., leads the global cold chain industry. With advanced infrastructure, strict food and drug regulations, and strong consumer demand, this region contributes over one-third of global cold chain logistics activity.
What gives North America an edge?
- Technological adoption: From AI-powered tracking to automated warehouses, North American companies are often early adopters.
- Regulatory pressure: Agencies like the FDA and USDA enforce stringent guidelines that require robust cold chain systems.
- Market size: The sheer size of the retail, healthcare, and agricultural sectors in the U.S. and Canada fuels demand for temperature-controlled solutions.
Strategic takeaways
If your business operates in or ships to North America:
- Invest in compliance — Regulations are strict and penalties are real. Follow guidelines like FSMA and DSCSA closely.
- Focus on efficiency — With intense competition, your cold chain operations must be lean and fast.
- Leverage tech hubs — Collaborate with startups or use smart logistics software that’s widely available in this market.
North America sets the tone for global standards. Align with it, and you’re future-proofing your business.
7. The Asia-Pacific cold chain market is growing at 12% CAGR, faster than any other region
The new growth frontier
Asia-Pacific is the fastest-growing cold chain region in the world. The 12% annual growth rate is powered by rising middle-class incomes, rapid urbanization, and demand for safer, higher-quality food and medicines.
Key drivers in Asia-Pacific
- Growing e-commerce — Especially in countries like China, India, and Indonesia.
- Government investment — Public-private partnerships are expanding cold storage in rural and urban areas.
- Export potential — Countries are exporting seafood, fruit, and pharma to the West, requiring cold chain readiness.
What should businesses do?
- Enter early — Emerging markets offer first-mover advantages if you can manage the risks.
- Partner locally — Work with regional players who understand the regulatory landscape and consumer behavior.
- Plan for diversity — Each country in Asia has different infrastructure levels. Customize your operations accordingly.
Don’t ignore Asia’s rise. The real cold chain action may soon shift eastward.
8. Frozen food demand has increased by 28% post-COVID, boosting cold chain infrastructure needs
From crisis to convenience
The pandemic changed the way people eat. Frozen food sales soared as consumers stocked up for longer periods and avoided frequent grocery visits. This 28% jump isn’t just a spike — it has sparked long-term changes in food logistics.
Why frozen food is here to stay
- Longer shelf life — Reduces food waste and shopping frequency.
- Improved quality — Frozen meals are no longer considered low-grade; brands have stepped up.
- New buying habits — Consumers are more open to online grocery shopping, especially for frozen items.
Implications for the cold chain
- More cold storage — Retailers and distributors need to expand freezer space.
- Last-mile delivery — Urban delivery models must adapt to include chilled and frozen transport.
- Packaging innovation — Better insulation and eco-friendly cold packs are in high demand.
If you’re in the food business, it’s time to think frozen — and keep it chilled from factory to fork.
9. IoT adoption in cold chain logistics is expected to grow by 17.4% annually through 2030
The rise of smart logistics
Internet of Things (IoT) is transforming how cold chains are monitored. With a 17.4% annual growth, the adoption of sensors, smart tags, and cloud-based monitoring systems is becoming standard, not optional.
What IoT can do for your cold chain
- Real-time tracking — Monitor temperature, humidity, and even vibration instantly.
- Predictive alerts — Avoid spoilage with early warnings if a fridge is malfunctioning.
- Data-driven audits — Keep clean, verifiable records to meet regulatory demands.
How to get started
- Pick scalable solutions — Start with one segment (e.g., outbound pharma shipments) before going all-in.
- Train your team — New tech is only effective when the staff knows how to use it.
- Monitor ROI — Watch for reduced spoilage rates and improved delivery compliance.
The smarter your cold chain, the more reliable your service — and the fewer losses you’ll incur.
10. Bluetooth Low Energy (BLE) tracking devices are now used in over 45% of pharmaceutical cold chains
The tiny tech with a big impact
BLE sensors have revolutionized how pharmaceuticals are monitored during transport. These small, battery-efficient devices now play a role in nearly half of all pharma cold chain systems.
Why BLE is winning
- Low power consumption — Sensors last weeks or months without needing a recharge.
- High accuracy — BLE can track minor changes in temperature and location.
- Easy integration — These devices work with smartphones, tablets, and cloud platforms.
What you can do with BLE
- Close visibility gaps — Know where your product is and what condition it’s in, every step of the way.
- Streamline compliance — Generate automatic reports for regulators or internal audits.
- Reduce costs — Preventive action is cheaper than replacing spoiled drugs.
If you handle pharmaceuticals, BLE tracking isn’t a nice-to-have — it’s your frontline defense against costly errors.
11. The food industry accounts for 45% of cold chain logistics revenue
Food’s cold dependency
Almost half of the cold chain industry’s revenue comes from transporting and storing food. From farm to shelf, keeping food fresh, safe, and appetizing is a temperature-controlled journey. Whether it’s dairy, meat, seafood, or ready-to-eat meals, cold logistics make it all possible.
Why food needs cold logistics more than ever
- Consumer expectations: People now expect fresh products, even if they’re shipped from far away.
- Food safety laws: Regulations have tightened globally, especially on meats and dairy.
- Export markets: Global food trade means perishables travel thousands of miles and need reliable chilling.
Action points for food businesses
- Build flexibility — Some foods need freezing, some need chilling. Your system must handle both.
- Check shelf-life impact — Know how temperature affects your products over time.
- Communicate freshness — Share cold chain certifications or handling procedures with retailers and customers.
When food is involved, freshness is everything. And in today’s competitive market, freshness is what sells.
12. 40% of cold chain losses are due to human error or poor training
The weakest link
Even with advanced tech, the cold chain still relies on people. A whopping 40% of losses happen because someone didn’t follow procedure, mishandled a product, or simply didn’t know what to do.
Common human-related errors
- Leaving doors open on refrigerated trucks or storage units
- Improper stacking that blocks airflow
- Manual data entry mistakes that go unnoticed until it’s too late
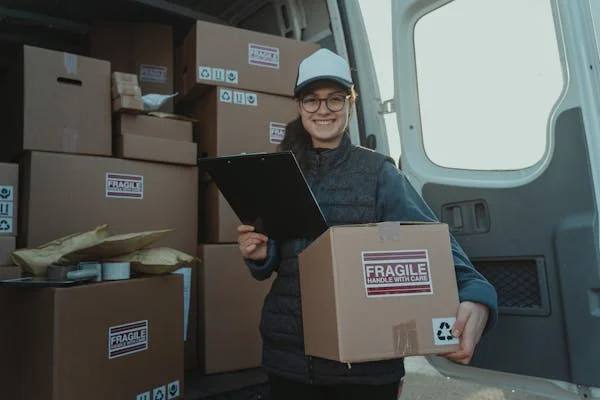
Training is your best defense
- Standardize procedures — Everyone should know how to handle temperature-sensitive products.
- Run simulations — Mock drills and emergency scenarios can prepare your team.
- Certify handlers — Programs like HACCP and GDP offer certifications that build credibility and reduce risk.
People can be your strongest asset — or your biggest liability. Choose wisely by investing in education.
13. Cold storage capacity globally exceeds 700 million cubic meters
A massive cold footprint
This stat reflects the massive infrastructure needed to keep the cold chain running. Over 700 million cubic meters of cold storage means facilities big and small, across the globe, are humming with activity every second.
What’s inside this cold space?
- Frozen goods like meat and seafood
- Chilled goods like dairy and fresh produce
- Ultra-cold items like certain biotech drugs and vaccines
What this means for businesses
- Space is competitive — Cold storage isn’t just about volume; it’s about location, temperature range, and efficiency.
- Automation is key — With such scale, manual operations can’t keep up. Use automation to reduce errors and boost throughput.
- Design smart — Warehouse layout affects airflow, loading speed, and energy usage.
Big numbers are impressive. But smart, optimized cold storage? That’s where the money is.
14. Machine learning and AI are predicted to reduce spoilage rates by up to 35%
Intelligence meets refrigeration
Machine learning and AI are no longer buzzwords — they’re being used in cold chain operations to predict spoilage risks, optimize routes, and automate temperature control. A potential 35% reduction in spoilage is a game-changer.
How AI makes the cold chain smarter
- Predictive analytics — Use past data to foresee equipment failures or risky routes.
- Smart routing — AI finds the quickest, safest, and most energy-efficient paths for delivery.
- Inventory forecasting — Reduce overstocking and understocking with demand-driven models.
Where to start with AI
- Integrate sensors — Data is the foundation. No AI works without it.
- Use dashboards — Visual tools help you act on AI insights in real time.
- Start with one use case — Route planning or warehouse temperature control are good starting points.
Spoilage isn’t just about ice and insulation. It’s about insight. And AI is bringing plenty of it.
15. Solar-powered cold storage units are expected to increase by 25% year-over-year in developing countries
Cold without the grid
In many rural or developing areas, consistent electricity is a challenge. That’s why solar-powered cold storage is rising fast — especially where traditional infrastructure is weak or absent.
Why solar cold storage matters
- Reduces losses for farmers — They can store perishable produce instead of watching it rot.
- Improves rural healthcare — Medicines and vaccines stay viable without grid dependency.
- Cuts energy costs — Especially important for regions with high electricity prices or frequent blackouts.
Actionable steps
- Explore off-grid options — Look for modular solar storage that’s plug-and-play.
- Combine with mobile tech — SMS alerts or app dashboards can help monitor storage from afar.
- Seek grants or partnerships — Governments and NGOs often fund such systems in underserved regions.
Innovation doesn’t always mean complex tech. Sometimes, it’s just smart simplicity powered by the sun
16. Real-time temperature monitoring adoption exceeds 65% in developed nations
Keeping a live eye on the chill
More than two-thirds of cold chain operations in developed markets now use real-time monitoring. That means they know exactly when a fridge dips below safe limits — and can act immediately.
Why real-time is the new standard
- Instant alerts — Stop a problem before it becomes a disaster.
- Continuous records — Essential for audits, especially in pharma or food.
- Trust-building — Retailers and regulators trust brands that prove their cold chain compliance.
How to implement it
- Pick flexible tech — Choose monitoring that works across trucks, warehouses, and packaging.
- Train your team — Real-time alerts are only useful if someone’s watching and ready to act.
- Integrate with ERP systems — Link temperature logs to your inventory and logistics data.
When the stakes are high, minutes matter. And real-time gives you those minutes back.
17. Cold chain failures result in $35 billion in annual losses globally
The true cost of failure
This staggering figure covers lost goods, replacement costs, regulatory penalties, and damaged reputation. $35 billion a year — just because the temperature slipped.
Where the losses occur
- Transport — Road and air shipping have the most breaches.
- Warehousing — Power outages or door mismanagement can wreak havoc.
- Last mile — Small-scale errors during delivery often go unnoticed until it’s too late.
What to do about it
- Audit often — Prevention is cheaper than correction.
- Improve packaging — Better insulation reduces the impact of short-term failures.
- Create a crisis protocol — Know what to do if your cooling system fails mid-shipment.
This stat isn’t just a warning. It’s a call to tighten every link in your chain.
18. Refrigerated trucks make up 15% of global freight vehicles
The backbone of the moving cold chain
Refrigerated trucks, also known as reefer trucks, are the workhorses of cold chain logistics. They carry everything from frozen meat to lab samples across cities, borders, and even continents. And while 15% may seem small, it’s a massive share considering the global size of the freight industry.

Why reefer trucks matter more than ever
- First and last-mile delivery: Warehouses and ports don’t bring food to homes. Trucks do.
- Cross-border consistency: Keeping the temperature stable across long distances is no small feat.
- Versatility: Whether you’re delivering groceries or blood plasma, reefer trucks are adaptable to different cold zones.
How to optimize your refrigerated fleet
- Regular maintenance: Poorly maintained trucks are the biggest cause of cold chain breaches.
- Use route optimization: Fewer delays mean less chance of temperature fluctuations.
- Fit them with IoT: Real-time tracking makes drivers and dispatchers more responsive.
Your cold chain is only as reliable as your trucks. Keep them efficient, and your products stay fresh all the way.
19. Cold chain logistics accounts for 16% of food waste globally
Waste we can prevent
A significant portion of global food waste — about 16% — can be traced back to failures in the cold chain. That’s spoiled vegetables, melted meat, and expired dairy that never reach the consumer, often because the temperature was off.
Why food goes to waste
- Inconsistent refrigeration at transport hubs
- Delays in customs or transit that break the cold cycle
- Inadequate rural cold storage in developing nations
What you can do to reduce it
- Map your pain points — Is spoilage happening in transit, or at storage?
- Strengthen weak links — Shorten lead times or improve equipment where needed.
- Work closely with farmers and suppliers — Help them invest in cold chain tools early in the supply process.
Reducing food waste isn’t just about being sustainable — it’s about saving money and improving supply chain trust.
20. Automated cold warehouses are projected to grow by 13.2% CAGR from 2024 to 2030
The future is (mostly) hands-free
Automation is making its way into every warehouse — and cold storage is no exception. With a projected 13.2% annual growth, automated systems are set to become standard in cold chain operations.
Benefits of automation in cold storage
- Faster picking and sorting — Robots don’t slow down in -20°C environments.
- Lower labor costs — Cold warehouses are tough work; automation fills gaps.
- Reduced errors — Machines don’t forget to close a freezer door.
How to get started
- Automate in stages — Begin with pallet movers or conveyor belts.
- Plan for retrofitting — You don’t need to build from scratch to modernize.
- Track ROI carefully — Measure labor savings, spoilage reduction, and throughput improvements.
Automation isn’t about replacing people. It’s about enhancing precision and speed in places where cold isn’t kind.
21. Over 70% of consumers consider cold chain integrity when purchasing perishable goods
Trust and transparency sell
Customers today are informed. They read labels, ask questions, and care deeply about how their food or medicine is handled. More than 70% consider cold chain integrity before making a purchase — especially for meat, dairy, and pharmaceuticals.
Why this matters to your brand
- Spoilage = lost loyalty — A bad experience means a lost customer.
- Certifications build trust — Sharing compliance credentials makes a difference.
- Transparency wins — Consumers prefer brands that can trace their product’s journey.
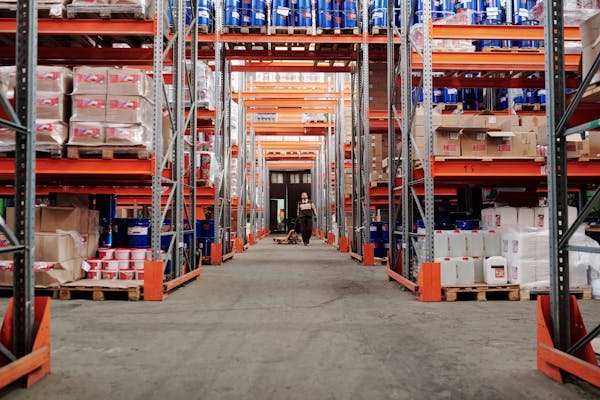
How to show cold chain integrity
- Use QR codes on packaging — Link them to storage or delivery data.
- Display temperature logs in-store or online.
- Work with certified logistics partners — Customers trust recognizable industry badges.
The cold chain is no longer just operational — it’s part of your brand story.
22. Dry ice is used in over 55% of pharmaceutical shipments for deep-freeze transport
The power of extreme cold
When pharmaceuticals need to be kept at ultra-low temperatures — like vaccines or biological samples — dry ice is the go-to solution. Its sublimation properties allow consistent cooling without melting, and that’s why over half of pharma shipments rely on it.
How dry ice supports pharma logistics
- Maintains temperatures below -70°C for extended periods
- Requires no electricity, making it ideal for remote or mobile shipping
- Evaporates cleanly, leaving no mess or contamination
Things to watch for
- Ventilation — Dry ice releases CO₂, which can be dangerous in closed spaces.
- Proper packaging — Insulation must complement the dry ice for extended cooling.
- Compliance — Shipping with dry ice requires hazardous material training in many regions.
Dry ice isn’t magical — but when handled right, it’s one of the most effective deep-freeze tools in logistics.
23. Temperature-controlled last-mile delivery is expected to increase by 20% annually
The final stretch is heating up
As consumer demand for fresh food and medicine delivery rises, the last mile — that crucial final step to the door — is under pressure. A 20% annual growth shows this isn’t just a trend. It’s the new norm.
Why the last mile is tricky
- Urban congestion delays deliveries and causes spoilage risks.
- Small orders need more specialized packaging and tracking.
- Consumer impatience means there’s no room for errors or delays.
How to build a reliable last-mile strategy
- Invest in micro-fulfillment centers — Small, local hubs reduce travel time.
- Use electric or insulated bikes — Perfect for short-range, eco-friendly deliveries.
- Enable real-time notifications — Keep the customer informed and ready to receive.
A weak last mile can ruin a perfect upstream supply chain. Strengthen it, and you’ll build lasting loyalty.
24. The average temperature breach threshold for vaccines is 2°C to 8°C
Precision matters
Vaccines are among the most sensitive items in the cold chain. Most must be kept strictly between 2°C and 8°C. Any fluctuation outside this range — even briefly — can render them ineffective.
Why such strict temperature ranges?
- Biological stability — The active ingredients break down when exposed to heat or freezing.
- Regulatory compliance — Distribution records must show zero excursions.
- Patient safety — Ineffective vaccines can lead to disease outbreaks and lawsuits.

What you must do
- Calibrate your sensors regularly to maintain accuracy.
- Avoid overstocking — Smaller batches are easier to control.
- Automate breach alerts — Human monitoring isn’t fast enough for life-saving cargo.
With vaccines, near enough is not good enough. The window is narrow, and the margin for error is zero.
25. Blockchain tracking systems in cold chain logistics are forecast to grow by 48% annually
Trust through transparency
Blockchain isn’t just for crypto anymore. It’s becoming a key player in cold chain logistics by offering an unchangeable record of every handoff, temperature reading, and delay. A 48% growth rate shows just how much the industry values verifiable transparency.
How blockchain helps cold chains
- Tamper-proof logs — You can’t change records without everyone seeing it.
- Clear accountability — Every checkpoint, every actor, every time stamp is tracked.
- Faster recalls — If a shipment goes bad, you can trace it back instantly and act fast.
Practical applications
- Track sensitive shipments like biologics or luxury foods
- Use smart contracts that automatically trigger actions like alerts or payments
- Share selective access — Let partners or regulators see only the data relevant to them
Blockchain isn’t just a buzzword. It’s a solution for one of cold chain logistics’ biggest challenges: trust.
26. Cold chain emissions represent 4% of total logistics-related CO₂ emissions
The cold chain’s carbon footprint
Refrigeration takes energy — a lot of it. Cooling systems, insulated vehicles, and deep-freeze warehouses all run on electricity or fuel. And that energy use adds up to 4% of global logistics emissions.
Why emissions are rising
- Increased demand for frozen and chilled goods
- Expansion into remote or hot regions
- Outdated refrigeration systems still in use across the globe
How to reduce your impact
- Switch to natural refrigerants like ammonia or CO₂, which have lower environmental impact
- Upgrade to energy-efficient equipment and solar-powered systems
- Use routing software to reduce fuel use and idling times
The future of the cold chain must be both efficient and environmentally responsible. A greener cold chain is not just a moral move — it’s a market advantage.
27. The global market for cold chain packaging is projected to reach $43 billion by 2030
Packaging that protects the chill
It’s not just about the truck or the fridge — it’s also about what goes around your product. Cold chain packaging is a booming industry, and rightly so. It’s often the first and last line of defense against temperature excursions.
Why packaging matters
- Controls micro-climate around the product
- Provides insulation during handovers or delays
- Improves delivery flexibility — especially in urban areas
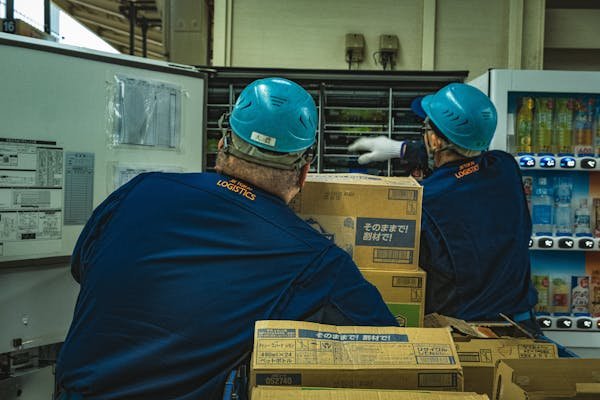
What to look for
- Validated performance — Make sure packaging can handle the journey duration and expected conditions
- Reusability — Reduce waste and cost by choosing returnable containers
- Compatibility with sensors — Some modern packaging includes tracking tech
Smart packaging isn’t just a box. It’s a temperature-regulating, data-reporting, product-saving shield.
28. Cold chain warehousing costs have increased by 15–20% since 2020
Cold storage is getting expensive
Since 2020, the demand for cold storage has surged, pushing costs up by 15 to 20%. This includes rent, utilities, labor, and equipment maintenance — all rising due to increased demand, energy prices, and tight supply.
Why it’s costing more
- Construction delays and material shortages
- Labor shortages in the logistics sector
- Higher energy costs in running large-scale refrigeration
How to control your costs
- Improve inventory turnover to avoid overstocking expensive space
- Use shared warehousing — Co-op models are growing in popularity
- Adopt energy-saving tech — Insulated panels, LED lighting, and efficient compressors make a difference
Cold chain is premium space — treat it like gold, not a garage.
29. Mobile cold storage units saw a 50% increase in usage during the COVID-19 pandemic
Flexibility in a crisis
During COVID-19, businesses needed to store perishables, vaccines, and test kits closer to end-users — and fast. Mobile cold storage became a lifesaver, with usage surging 50% in just a year.
Why mobile units matter
- They’re fast to deploy — No permits or construction needed
- They’re location-flexible — Move them where the demand is
- They’re cost-effective short-term — Great for spikes or seasonal needs
When to use mobile cold storage
- During seasonal demand — Like holiday food surges or summer vaccine drives
- For remote operations — Events, clinics, or emergency responses
- While upgrading your warehouse — Keep operations running without interruption
Flexibility is a competitive edge — and mobile cold storage delivers it in full.
30. Smart thermometers and sensors are expected to be in use in 80% of cold storage units by 2026
From manual checks to smart sensing
Gone are the days of paper logs and clipboard checks. Smart sensors are quickly becoming standard, with 80% adoption expected by 2026 in cold storage units worldwide.
Benefits of smart sensors
- Constant vigilance — They don’t sleep, miss a reading, or forget to report
- Automated alerts — Instantly notify you of risk before spoilage happens
- Cloud integration — Access data remotely, anytime
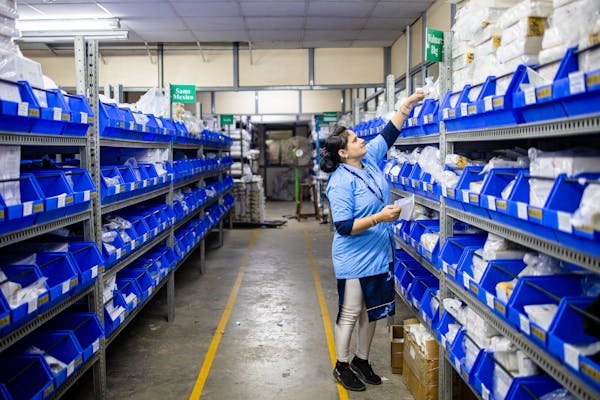
Getting started
- Start with high-risk zones — Freezers, vaccine rooms, or reefer docks
- Choose scalable platforms — So you can expand later without system overhauls
- Integrate with your ERP or TMS — For full cold chain visibility
The best part? Smart sensors pay for themselves by preventing just one major spoilage incident.
Conclusion
The cold chain logistics industry is more than just refrigeration. It’s about people, technology, timing, and trust — all working together to deliver products that matter. Whether you’re shipping strawberries or stem cells, your success depends on staying ahead of the trends that are reshaping the cold supply chain world.